Smart Inventory Management
Smart Inventory Management systems leverage advanced technology, such as artificial intelligence (AI), machine learning, cloud computing, and IoT (Internet of Things), to automate, optimize, and streamline inventory processes. These systems help businesses reduce errors, improve accuracy, and enhance efficiency in tracking, ordering, and managing stock. Below are the key features of Smart Inventory Management systems:
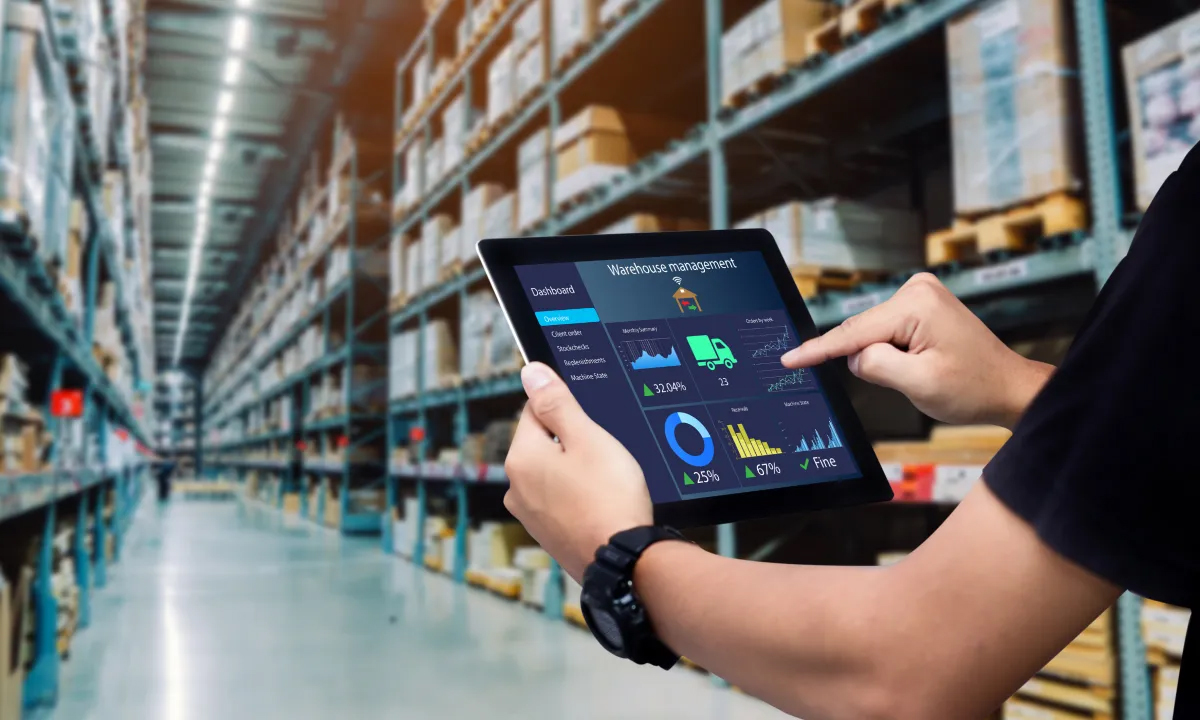
Real-Time Inventory Tracking
- Live Stock Monitoring: Track stock levels in real time across multiple locations (warehouses, retail stores, distribution centers) using sensors, RFID tags, or barcode scanners.
- Instant Updates: Automated updates to inventory counts when items are sold, returned, moved, or restocked, ensuring accurate data at all times.
- IoT Integration: Use connected devices (RFID tags, smart shelves) to track products and monitor their movement in real time.
Automated Stock Replenishment
- Low Stock Alerts: Automatically notify managers or the system when stock levels fall below predefined thresholds to prevent stockouts.
- Replenishment Orders: Automatically trigger restocking orders from suppliers based on inventory levels and demand predictions.
- Lead Time Optimization: Consider supplier lead times and order delivery schedules to optimize the timing of replenishment orders.
Demand Forecasting
- AI-Powered Analytics: Use machine learning algorithms to analyze historical sales data and predict future demand, helping businesses prepare for seasonal fluctuations or unexpected surges.
- Sales Trends Analysis: Track trends over time to identify patterns in customer demand, improving purchasing decisions and stock levels.
- Inventory Turnover Prediction: Estimate how quickly products will sell, helping you to adjust procurement strategies for high-turnover vs. slow-moving items.
Barcode & RFID Scanning
- Barcode Scanners: Use barcode scanners to quickly track product movement in and out of stock, improving accuracy and speed.
- RFID Tracking: Employ RFID technology to automate the tracking of products without needing to manually scan barcodes, ensuring faster and more reliable data capture.
- Mobile Inventory Management: Use mobile devices or tablets to scan barcodes or RFID tags and update inventory data directly from the warehouse floor.
Automated Reordering
- Custom Reordering Rules: Set rules for automatic reordering based on factors like sales velocity, seasonal trends, and supplier availability.
- Order Forecasting: Predict the optimal reorder quantity for each product based on demand forecasts and historical sales data.
- Supplier Management: Integrate with supplier systems to automate orders and ensure timely deliveries, helping to maintain stock levels without over-purchasing.
Inventory Auditing and Reconciliation
- Automated Audits: Conduct regular or ad-hoc inventory audits using smart devices (e.g., RFID) to ensure that physical stock matches the recorded data in the system.
- Cycle Counting: Perform ongoing, smaller-scale stock counts (instead of full inventory counts) to detect discrepancies in real time.
- Real-time Reconciliation: Automatically reconcile any discrepancies between physical inventory and system records, minimizing manual effort and reducing human error.
User and Access Control
- Role-Based Permissions: Assign different levels of access to users based on their role in the inventory process (e.g., stock manager, warehouse worker, admin).
- Audit Trails: Maintain a detailed log of who made changes to inventory records, enhancing accountability and reducing fraud.
- Inventory Alerts and Notifications: Set up alerts for specific users for low stock levels, shipment delays, or order discrepancies.
Mobile and Cloud-Based Access
- Cloud Integration: Access inventory data from anywhere, anytime, using a cloud-based platform, ensuring businesses have real-time information.
- Mobile App Integration: Use mobile apps to update inventory, check stock levels, place orders, or perform audits directly from smartphones or tablets.
- Offline Functionality: For environments with limited internet connectivity, offline capabilities allow users to continue working and sync data when they go online.
Integration with Other Systems
- E-commerce Platforms: Integrate with platforms like Shopify, WooCommerce, Magento, or Amazon to automatically update inventory based on online sales.
- Accounting Software: Integrate with accounting tools like QuickBooks or Xero to track inventory-related expenses and cost of goods sold (COGS).
- POS Systems: Sync with Point of Sale systems to ensure that stock levels are updated automatically when sales occur in-store or through a POS terminal.
Multi-Location and Multi-Warehouse Management
- Centralized Dashboard: Manage inventory across multiple warehouses, stores, or distribution centers from a single interface.
- Stock Transfer: Automate the process of transferring stock between locations when there’s excess in one place and a shortage in another.
- Geo-Location Optimization: Optimize inventory placement based on regional demand to reduce shipping time and costs.
Inventory Optimization
- Min-Max Levels: Set minimum and maximum inventory levels for each item, ensuring that there is enough stock to meet demand without overstocking.
- Just-In-Time (JIT) Inventory: Implement JIT principles to ensure that stock is ordered and delivered just before it is needed, reducing excess inventory and storage costs.
- ABC Classification: Classify inventory into categories (A: high-value/fast-moving, B: moderate, C: low-value/slow-moving) to prioritize management efforts.
Supplier and Vendor Management
- Vendor Performance Tracking: Monitor supplier performance, including delivery times, product quality, and price competitiveness, to improve decision-making when reordering stock.
- Automated Purchase Orders: Automatically generate purchase orders (POs) and send them directly to suppliers when stock levels fall below the reorder point.
- Lead Time Tracking: Monitor the lead times for each supplier to ensure that orders are placed at the right time for on-time deliveries.
Batch and Expiry Date Management
- Batch Tracking: Track inventory in batches, ensuring that products are grouped by production or purchase lot and can be traced for quality control.
- Expiration Date Monitoring: Keep track of products with limited shelf life, ensuring that older items are used or sold first (FIFO – First In, First Out).
- Product Recall Management: Quickly identify and recall products in the event of a defect or safety issue based on batch and expiry date data.
Analytics and Reporting
- Inventory Performance Reports: Generate reports on key performance indicators (KPIs) such as stock turnover rate, out-of-stock frequency, and slow-moving items.
- Cost Analysis: Analyze inventory costs, including procurement, storage, and wastage, to identify cost-saving opportunities.
- Profit Margin Insights: Track product performance and margins, helping businesses focus on profitable products and manage less profitable ones.
Customer Order Management
- Order Fulfillment: Use real-time inventory tracking to ensure customer orders are fulfilled promptly and accurately.
- Backorder Management: Manage backorders and notify customers if items are out of stock, offering alternatives or estimated delivery dates.
- Multi-channel Integration: Sync inventory across online stores, brick-and-mortar locations, and third-party marketplaces to provide accurate stock information to customers.
Conclusion
Smart Inventory Management systems enable businesses to optimize their supply chain, reduce costs, improve efficiency, and enhance customer satisfaction. By automating tasks such as stock tracking, replenishment, and order management, and utilizing advanced technologies like AI and IoT, these systems provide businesses with real-time insights, predictive capabilities, and seamless integration with other business functions. These features contribute to improved inventory accuracy, reduced waste, and better decision-making, ultimately driving growth and profitability.